Concrete Contractor
By Tua Lino
What standard specifications should I know or understand regarding information received from a contractor in anticipation of signing a contract to have my concrete driveway replaced? What is better rebar, reinforcement mesh and fiberglass reinforced cement? Depth of the driveway poured, 2 inches 4 or more? How far should expansion joints be put in to handle heat and cold.
Reinforcement steel in flatwork is strictly for crack control. The best crack control is affected by putting the steel in the upper half of the slab. If your contractor can guarantee he will keep the wire mesh in the upper half of the concrete, that will do as well as rebar. Make sure he gives at least 3/4 inch cover to whatever reinforcement he uses.
The standard driveway depth is 4 inch, but that doesn’t mean that depth is right for you. It really depends on the soil conditions and the load you will be putting on the concrete. Thickened edges (beams) are highly recommended for the outsides of the driveway. This will enable the edges to take that occasional load on the edge or coming onto or off of the edge.
Normal Portland cement concrete likes to crack every 10-12 fee, so jointing in all directions no more than 10 feet, with the joints being a minimum of 1/4 the slab depth, should help the expansion/contraction problem. There are two types of joints: contraction and construction. Contraction joints are usually installed with a concrete saw after the concrete gets hard or a jointing tool while the concrete is still fresh. Construction joints are preinstalled dividers such as redwood strips, aluminum keyways, or other physical barriers. Either type of joint will allow for expansion/contraction, so if you don’t want redwood every 10 feet, you don’t have to have it. Make your joints as square as you can. Try to avoid rectangular jointing sections. Make sure the contractor orders concrete that has 4-6% entrained air, since you live in conditions that probably require salting of roads. The air will enhance the concrete’s freeze/ thaw durability and make it less susceptible to salt damage.
I could spend at least 8 hours going over things to look out for and things to avoid. The main thing is sitting down with the contractor before you sign a contract, and tell him how you want the thing to look when he gets finished. Discuss whether visible cracks are acceptable or not. Discuss a warranty. Tell them what you want in the end, put it in your contract, then get out of his way and let him give you what you want. If he doesn’t give you what he says he would in the contract, you have legal standing for a remedy. Also, let him buy the concrete so he can’t blame you for buying an inferior product that he couldn’t work with.
About the Author
|
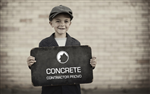 | Tua Lino, Concrete Contractor Provo 943 N 1050 W Provo, UT 84604 8013807444
Contact Author: request info
If you would like to re-print this article, please contact the author.
|
|
|
|
|
|